در دنیای امروز، ما به طور کامل به برق و دادهها وابسته هستیم. از روشنایی خانههایمان تا تامین انرژی وسایل الکترونیکی، از برقراری ارتباط با جهان از طریق اینترنت تا انتقال اطلاعات در شبکههای عظیم، همه اینها به سیم و کابل متکی هستند. اما شاید تا به حال به این موضوع فکر نکرده باشید که این سیمها و کابلها چگونه ساخته میشوند؟ چه مراحلی را طی میکنند تا از دل معادن و کارخانهها به خانهها و محل کار ما برسند؟
در این مقاله، سفری به دنیای مراحل تولید سیم و کابل خواهیم داشت. گام به گام، مراحل مختلف این فرآیند پیچیده را از استخراج مواد اولیه تا تولید نهایی محصول نهایی بررسی خواهیم کرد. تا انتهای مطلب با ما همراه شوید.
مواد اولیه سیم و کابل
در ساخت سیم و کابل از مواد اولیه مختلفی استفاده میشود که هر کدام نقش خاصی به خود را دارند. در ادامه به بررسی مهمترین مواد اولیه به کار رفته در مراحل تولید سیم و کابل و نقش هر کدام میپردازیم:
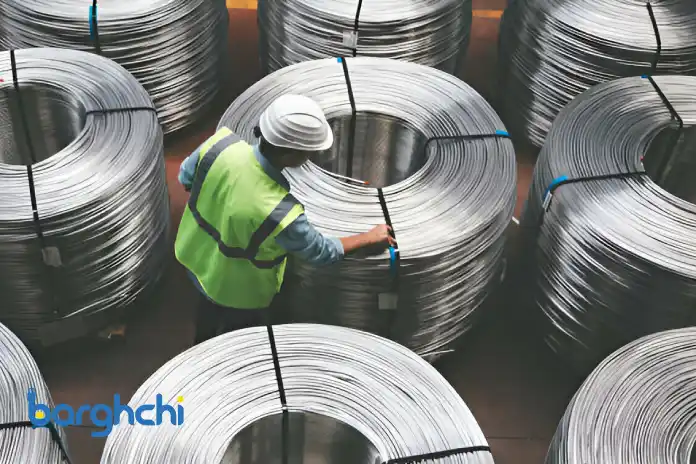
مواد اولیه سیم و کابل
- مس: رسانای الکتریکی بسیار عالی با انعطافپذیری بالا، مقاوم در برابر خوردگی و با طول عمر زیاد. به دلیل این خواص، رایجترین هادی در سیم و کابل است.
- آلومینیوم: سبکتر و ارزانتر از مس، اما با رسانایی الکتریکی کمتر. به طور کلی در کابلهای با ولتاژ پایین و جریان بالا استفاده میشود.
- پلاستیک: پلاستیک مادهای سبک است که وزن سیم و کابل را به طور قابلتوجهی کاهش میدهد. این ویژگی، حمل و نقل و نصب سیم و کابل را آسانتر میکند. علاوهبر این مادهای ارزان است که قیمت نهایی سیم و کابل را کاهش میدهد. این ماده عایق الکتریکی خوبی است که از عبور جریان الکتریکی از غلاف به هادی جلوگیری میکند که این ویژگی، ایمنی سیم و کابل را افزایش میدهد.
- لاستیک: لاستیک مادهای انعطافپذیر است که به راحتی خم شده و به اشکال مختلف درمیآید. این ویژگی، امکان ساخت سیم و کابل با انعطافپذیری بالا و قابلیت نصب در مکانهای مختلف را فراهم میکند. علاوهبر این لاستیک در برابر حرارت مقاوم است و میتواند دمای بالا را تحمل کند که امکان استفاده از سیم و کابل در محیطهای گرم و صنعتی را فراهم میکند.
- فولاد: فولاد فلزی بسیار مستحکم و مقاوم در برابر فشار، کشش و ضربه است. این ویژگی، فولاد را برای استفاده در کابلهایی که در معرض تنش مکانیکی بالا هستند، مانند کابلهای زیرزمینی و سفت، ایدهآل میکند. کاربرد اصلی فولاد در سیم و کابل، در ساخت آرمور است. آرمور از فولاد ساخته شده و وظیفه محافظت از هادی و عایق در برابر آسیبهای مکانیکی را بر عهده دارد.
نام ماده | مزایا | معایب | کاربرد |
مس | رسانایی بالا،انعطافپذیری، مقاومت در برابر خوردگی | گران | سیم برق، کابل مخابرات، کابل فشار قوی |
آلومینیوم | سبک، ارزان | رسانایی پایینتر | کابل فشار ضعیف، کابل هوایی |
لاستیک | انعطافپذیری، مقاومت در برابر حرارت، عایق الکتریکی | گران | کابل صنعتی |
پلاستیک | سبک، ارزان، عایق الکتریکی، مقاوم در برابر رطوبت | شکنندگی در دمای پایین، مقاومت کم در برابر حرارت | عایق سیم برق خانگی، کابل مخابرات |
فولاد | استحکام | رسانایی پایین،وزن،زنگ زدگی | آرمور،سیمهای مفتولی، افزایش استحکام هادی |
دستگاههای مورد نیاز برای تولید سیم و کابل
در صنعت تولید سیم و کابل، از دستگاههای مختلفی برای انجام مراحل مختلف فرآیند تولید استفاده میشود. این دستگاهها با توجه به نوع سیم و کابل تولیدی و ظرفیت تولید کارخانه میتوانند متفاوت باشند. اما به طور کلی ماشینآلات و دستگاههای مورد نیاز برای مراحل تولید سیم و کابل عبارتند از:

دستگاههای مورد نیاز برای تولید سیم و کابل
- دستگاه کلاف بازکن: وظیفه این دستگاه باز کردن قرقرههای مفتول مسی، آلومینیومی یا فولادی و صاف کردن آنها برای مراحل بعدی است.
- دستگاه کشش راد: مفتول را به طور پیوسته از کلاف بازکن میکشد و آن را نازکتر میکند.
- دستگاه آنیل: مفتول را در دمای مشخصی گرم میکند تا تنشهای داخلی آن را از بین ببرد و شکلپذیری آن را افزایش دهد.
- دستگاه فاین: مفتول را به طور پیوسته نازکتر میکند و آن را برای هادی نهایی آماده میکند.
- دستگاه بانچر: رشتههای هادی نازک شده را به هم میتاباند تا هادی نهایی با قطر و مشخصات مورد نظر تولید شود.
- دستگاه اکسترودر: عایق و روکش را به صورت مذاب روی هادی میپوشاند.
- دستگاه خنککننده: عایق و روکش را خنک و جامد میکند.
- دستگاه چاپ: اطلاعات مربوط به کابل مانند نوع، ولتاژ و تاریخ تولید را روی عایق چاپ میکند.
- دستگاه کشش: کابل را با کشش مشخص میکشد تا صاف و همتراز شود.
- دستگاه استرندر: رشتههای عایقدار شده را به هم میتاباند تا ساختار نهایی کابل ایجاد شود.
- دستگاه جمع کننده: کابل را به صورت کلاف یا قرقره جمع میکند.
- دستگاه تست: کیفیت و عیب و نقص کابل را از نظر پارامترهایی مانند عایق، هادی و ابعاد بررسی میکند.
- دستگاه بسته بندی: کابل را برای حمل و نقل و فروش بسته بندی میکند.
مراحل تولید سیم و کابل
تولید سیم و کابل برق یک فرایند پیچیده و دقیق است که نیاز به تجهیزات و مواد اولیه مناسب دارد. در ادامه، مراحل تولید سیم و کابل برق را از صفر تا صد بررسی میکنیم. مراحل تولید سیم و کابل از 7 بخش تشکیل میشود که این مراحل به شرح زیر است:
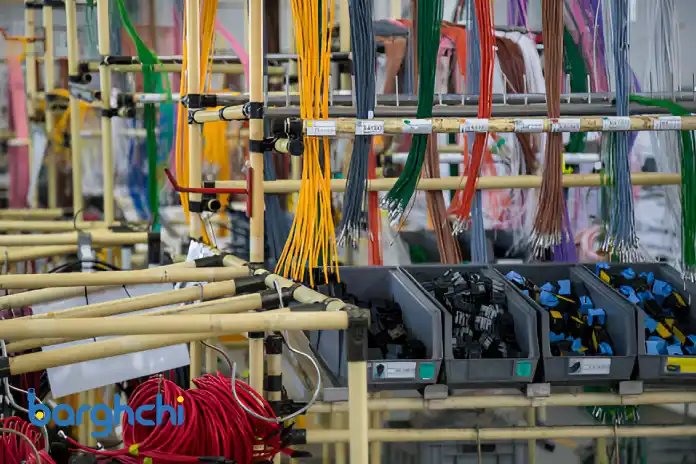
مراحل تولید سیم و کابل
- نازک کاری سیم و کابل
- آنیل کاری
- بانچ یا استرند کردن رشته های سیم
- عایق کاری
- روکش زنی + کراسلینک
- بسته بندی سیم و کابل
- بررسی نهایی
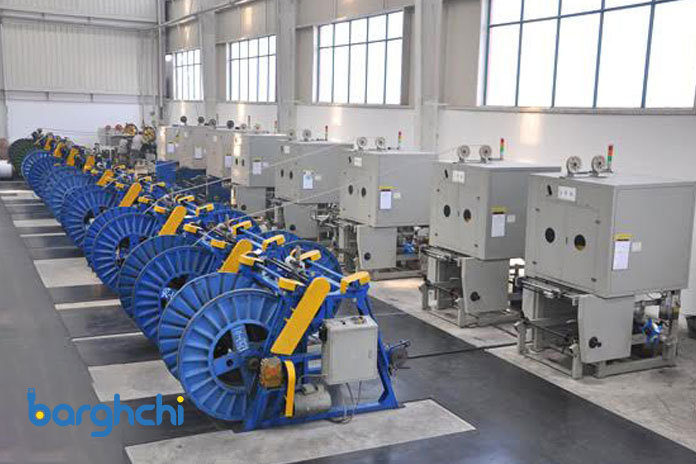
مراحل تولید سیم و کابل
مرحله 1: نازک کاری سیم و کابل
مواد اولیه سیم و کابل که معمولاً به صورت قطعات یا نوارهای ضخیم از فلزات هستند، توسط دستگاههای نازک کاری به قطرهای دلخواه تبدیل میشوند. برای مثال دستگاه سنگین راد وظیفه دارد تا یک لایه مفتول از جنس مس با ضخامت 8 میلیمتری را به یک مفتول نازکتر به ضخامت 1.38 میلیمتر تبدیل کند. دستگاههای نازک کاری از قالبهای مختلفی برای تغییر شکل مواد اولیه استفاده میکنند.
عملیات نازک کاری سیم و کابل توسط یک دستگاه نازککن راد و دستگاه نازککن فاین در دو مرحله صورت انجام میشود. به طور مثال، برای نازک کاری مس، از قالبهای دایموندی یا تنگستنی استفاده میشود. در این مرحله، مقاومت و خواص مکانیکی سیم و کابل بهبود مییابد.
بیشتر بخوانید: 5 عامل موثر در انتخاب نوع سیم و کابل
مرحله 2: آنیل کاری
در این مرحله، سیم و کابل نازک شده توسط دستگاههای آنیل کاری گرم میشوند تا خواص الکتریکی و مکانیکی آنها بهینه شود. همه مفتولهایی که در دستگاه فاین نازک شدند، در جایی معین کنار کوره آنیل کاری، بر اساس تابلوی مربوطه جمع شدند و وقتی به کمترین تعداد لازم برای آنیل کاری (۵۴ قرقره) رسیدند، برای وارد شدن به کوره و آنیل شدن آماده شدند.
آنیل کاری یک فرایند حرارتی است که باعث کاهش سختی، افزایش دوکیلیتی و کاهش مقاومت الکتریکی سیم و کابل میشود. در این مرحله، دما، زمان و جریان گازهای محافظ باید با دقت کنترل شود.
مرحله 3: بانچ یا استرند کردن رشتههای سیم
این فرایند با استفاده از دستگاه بانچر انجام میشود. ماده اولیه این مرحله مفتولهایی است که روی قرقرهها قرار دارند و آنیل شدهاند که تعداد و قطر آنها با سفارش مشتری و استاندارد مربوطه همخوانی دارد. برای ساخت کابلهای چند رشتهای مانند خودنگهدار، قدرتی نیاز است تا رشتههای متفاوت کابل با یک ساختار منظم به هم پیچیده شوند که این کار با دستگاه تابنده صورت میگیرد. در کابلهای خودنگهدار رشته اصلی که نقش تحمل بار کابل را دارد در مرکز قرار میگیرد و سایر رشتهها با طول و جهت پیچش مشخص به دور آن میچرخند.
مفتولهایی که با اندازه مشخص کشیده شدند روی قرقرههای ۶۳۰ جمع میشوند و برای بارگذاری روی دستگاه استرندر آماده میشوند، استرندرها مسئولیت بافتن هادیهای آلومینیومی را تا ۶۱ رشته دارند. کارکرد آنها به این شکل است که یک رشته مفتول به عنوان مغزی در میانه قرار میگیرد و به ترتیب ۶/۱۲/۱۸/۲۴ رشته مفتول به صورت چپگرد یا راستگرد، با چرخاندن استرندر و طول پیچش معینی که توسط جعبه دنده قابل تغییر است به دور مغزی میپیچند.
رشته پیچیده شده از یک قالب عبور میکند که این فرآیند، شکلگیری هادیهای خارجی اعم از کمپکت و یا سکتور کردن هادی را بر عهده دارد. گام بعد کمپکت کردن است، کمپکت کردن باعث میشود که فضای خالی و حفرههای بین رشتههای پیچیده شده از بین برود که در نتیجه سطح مقطع هادی را کاهش میدهد. هادی تولید شده پس از خارج شدن از روی کپستن وارد تیک آپ (جمع کن) میشود و به صورت منظم دور قرقره پیچیده میشوند.
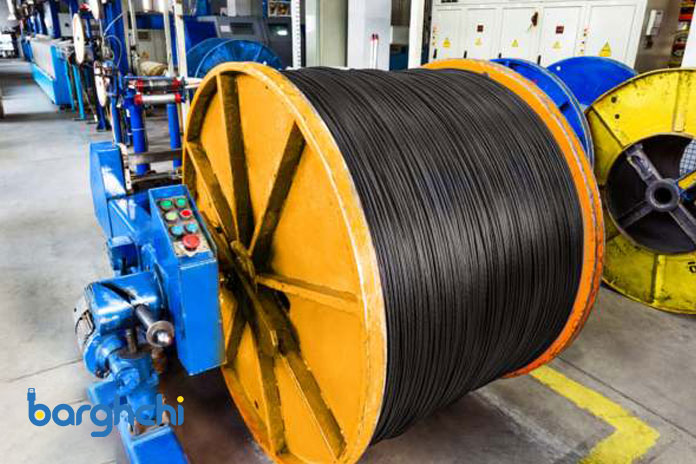
بانچ یا استرند کردن رشتههای سیم
مرحله 4: عایق کاری
سیم و کابل بانچ یا استرند شده توسط دستگاههای عایق کاری با یک یا چند لایه از مواد عایق پوشانده میشوند تا از نشت جریان الکتریکی جلوگیری شود. عایق کاری یک فرایند شیمیایی است که باعث کاهش خطر ایجاد شراره، آتش سوزی و صدمات به افراد و تجهیزات میشود. در این مرحله، نوع، ضخامت و رنگ مواد عایق باید با دقت انتخاب شود.
بیشتر بخوانید: آموزش سیم کشی برق ساختمان (0 تا 100)
مرحله 5: روکش زنی + کراسلینک
این مرحله با استفاده از دستگاه اکسترودر انجام میشود. دستگاه اکسترودر یک دستگاه صنعتی است که برای شکلدهی به مواد پلاستیکی با استفاده از حرارت و فشار استفاده میشود. مواد لازم در این مرحله شامل گرانول روکش، زیرههای بافته شده، پودر تالک و … میشود. پلاستیکهای فشاری با استفاده از دستگاه اکسترودر و نیرویزده شده، درون قالبهای دستگاه ریخته میشوند.
این دستگاه هم تغذیه گرم و هم تغذیه سرد دارد. در کابلهای قدرت باید رشتههای بافته شده در دستگاه اکسترودر با یک لایه از مواد پلیاتیلن یا PVC پوشانده شوند. این لایه نقش حفاظت مکانیکی از کابل را بر عهده دارد.
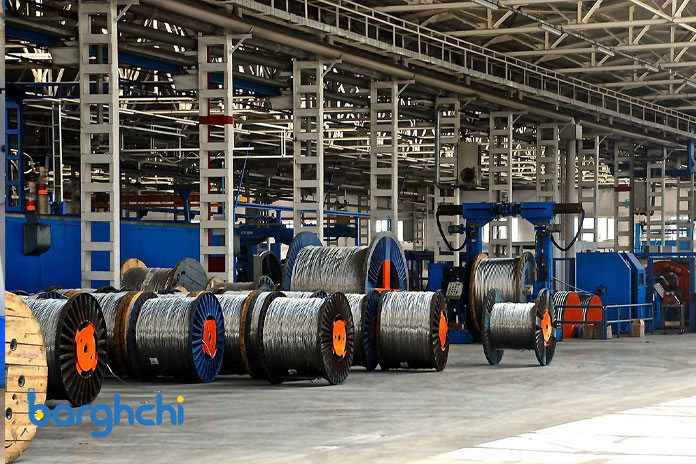
روکش زنی + کراسلینک
مرحله 6: بستهبندی سیم و کابل
در این مرحله، سیم و کابل روکشزده شده توسط دستگاهها به صورت رول، بابین، کارتن و غیره بستهبندی میشوند تا آماده حمل و نقل و انبارداری شوند. بستهبندی یک فرایند فیزیکی است که باعث حفظ شکل، اندازه و کیفیت سیم و کابل میشود. در این مرحله، نوع، ابعاد و وزن بستهبندی باید با دقت مشخص شود.
مرحله 7: بررسی نهایی
آخرین گام از مراحل تولید سیم و کابل برق مربوط به بررسی نهایی است. در این مرحله از کار سیم و کابل بستهبندی شده توسط دستگاهها و کارشناسان مورد آزمون و کنترل کیفی قرار میگیرند تا از رعایت استانداردها و مشخصات فنی مطمئن شوند. بررسی نهایی یک فرایند تجزیه و تحلیلی است که باعث افزایش اطمینان، اعتبار و امنیت سیم و کابل میشود. در این مرحله، آزمونهای مختلفی مانند آزمون ولتاژ بالا، آزمون مقاومت الکتریکی هادی و غیره انجام میشود. که در ادامه با این دو نمونه از آزمونها بیشتر آشنا خواهید شد.
بیشتر بخوانید: تفاوت کابل ابزار دقیق و کابل کنترل
آزمون ولتاژ بالا
آزمون ولتاژ بالا یک آزمون ایمنی الکتریکی است که برای سنجش صحت عملکرد و کیفیت عایق تجهیزات الکتریکی انجام میشود. در این آزمون، تجهیزات الکتریکی تحت ولتاژ بسیار بالاتر از ولتاژ عادی قرار میگیرند و جریان نشتی آنها اندازهگیری میشود.
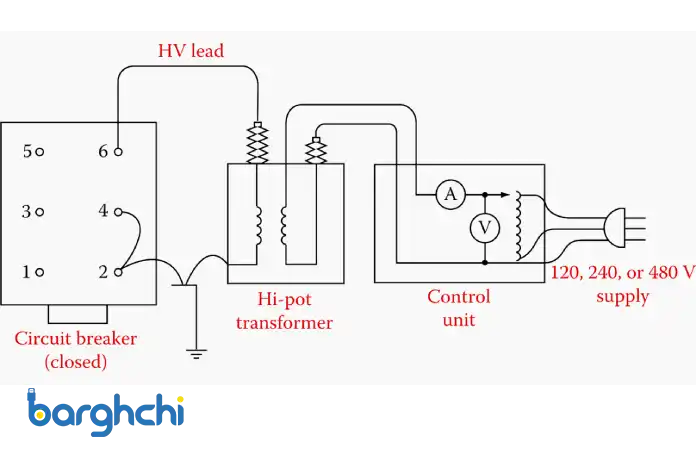
آزمون ولتاژ بالا
اگر جریان نشتی کمتر از حد مجاز باشد و پدیده شکست دی الکتریک رخ ندهد، آزمون با موفقیت به پایان میرسد. این آزمون برای تمامی تجهیزات الکتریکی الزامی است و بر اساس استانداردهای ملی و بینالمللی مانند IEC ۶۰۳۳۵ و IEC ۶۱۰۱۰ انجام میشود.
آزمون مقاومت الکتریکی هادی
آزمون مقاومت الکتریکی هادی یک آزمون کیفیت سیم و کابل است که برای سنجش مقاومت الکتریکی هادیها مطابق استانداردهای ملی و بینالمللی انجام میشود. در این آزمون، مقاومت هادی هر یک از رشتههای نمونه کابل، با استفاده از قانون اهم، محاسبه جریان و ولتاژ در سراسر نمونه، اندازهگیری شده و گزارش میشود.
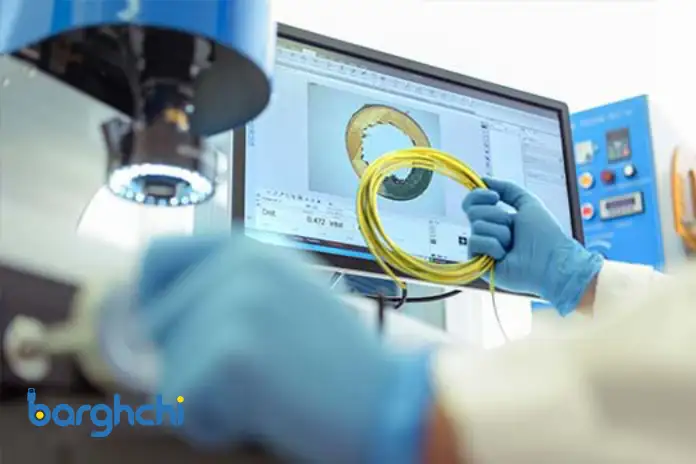
آزمون مقاومت الکتریکی هادی
آزمون مقاومت الکتریکی هادی به این دلیل انجام میشود که از مطابق بودن با مشخصات فنی و مقاومت الکتریکی سیم و کابل مطمئن شوند. این آزمون به افزایش کارایی، اطمینان و امنیت سیم و کابل کمک میکند. همچنین این آزمون میتواند نشان دهنده کیفیت مواد اولیه، فرایند تولید و عملکرد سیم و کابل باشد.
بیشتر بخوانید: علائم اختصاری سیم و کابل
نتیجه گیری
تولید سیم و کابل فرآیندی پیچیده و چند مرحلهای است که نیازمند تجهیزات و تخصص بالاست. در این مقاله، به طور مختصر به مراحل اصلی تولید سیم و کابل و دستگاههای مورد استفاده در هر مرحله اشاره شد. انتخاب مواد اولیه باکیفیت و استفاده از ماشینآلات مدرن و پیشرفته نقش مهمی در تولید سیم و کابل با کیفیت بالا دارد. رعایت استانداردهای ملی و بینالمللی نیز در تولید این محصول حائز اهمیت است. امید است که این مقاله برای شما مفید بوده باشد.
دیدگاه شما
اولین نفری باشید که نظر میدهید